Sluishuis, Amsterdam, the Netherlands
SLOPING FIRE-RESISTANT GLAZING FOR REMARKABLE SLUISHUIS
Author: Marco Groothoff
The Sluishuis rises at the place where city, countryside, and water come together in Amsterdam. This 46,500-square-metre housing project being built by the BIG - Bjarke Ingels Group and Barcode Architects will soon rise over the water. Which was reason enough to provide the windows of the cantilevered apartments with walkable fire-resistant glass with the highest classification (EI60). The installation of the glass was completed in November and the completion of the complex is scheduled for mid-2022.
The design of the Sluishuis, which will rise over the water near the Enneüs Heerma Bridge, is a nod to traditional inner-city courtyards. By tilting a corner of the block toward the water creates an inner courtyard that connects to the surrounding water and offers scenic views of the IJmeer (a bordering lake). In the vicinity of Steigereiland, the block slopes down in steps, which creates terraces and pleasantly 'scales' the building in proportion to the surrounding area. All apartments receive plenty of daylight illumination due to the shape of the building. Both residents and visitors can use the courtyard, the pontoon promenade around the building, and the public walkway to the top of the Sluishuis.
ASYMMETRIC
When you look at the floor plan, the structure looks like a traditional rectangular building block. But if you look at it from any other viewpoint, the building suddenly takes on a completely asymmetric character. A series of islands with houseboats and floating gardens will surround the building. The ground floor has a variety of facilities that include a central lobby for residents, a sailing school, a water sports centre, and a restaurant. The building will have 442 apartments that are intended for different target groups, income levels, and age groups. All homes are accessible via the central courtyard. Special float-in and water sports apartments are located on the ground floor. The other floors have a diversity of residences, from apartments with outdoor spaces and water views to penthouses with front gardens opening onto the courtyard.
The Sluishuis will be a passive building with an Energy Performance Coefficient (EPC) of -0.01. This means that the building produces more energy than it uses. The building's heating requirements were minimised by combining insulation techniques, triple glazing, heat recovery from the ventilation systems, and waste water collection. District heating and heat pumps for hot water and cooling also reduce energy consumption even more. About 2,200 square metres of solar panels offset the remaining energy consumption for heating, heat pumps, ventilation, and LED lighting.
MC KERSTEN
Ronald Struik is the project leader/installation manager at MC Kersten in Amsterdam. This company specialises in conceiving and developing complex metal structures, stairs, elevator shafts, fencing, window frames, doors and, works of art. Kersten is a family business founded in 1959 under the leadership of Robert and Jeroen Kersten, the sons of the founder. In the meantime, a third generation now also works at the company. 'The Sluishuis fire-resistant windows is in keeping with our series of special projects,' says Struik. 'It was a terrific collaboration with AGC Pyrobel who supplied walkable EI60 glazing for the windows in the apartments that slope over the water. There are a total of 42 frames that were precast at our production facility. We incorporated the glass into a Jansen VISS Fire profile. And the composition was specially tested for this application. This all sounds simple enough, but it certainly wasn't. There was the fire resistance and walkability and, for instance, the required high-quality airtightness to handle the massive energy performance of the building.'
With VISS Fire, Jansen offers a universally applicable, insulated, and modular façade construction system. The standard system is suitable for vertical interior and exterior walls rated for all fire resistance classes (E30, EW30/60/90, and EI30/60/90). An important feature is the small viewing width of 50 millimetres for the post and batten structures. The construction depths are 50 to 140 millimetres. This makes the profile system suitable for façade elements that exceed floors of up to a height of 5 metres and an unlimited width. In the Sluishuis, the window frame dimensions are 1,250 x 3,000 millimetres. 'The requirement of 60 minutes of fire resistance with the highest classification EI,' explains Struik, 'is based on need to prevent fire spreading from one apartment to another that are located diagonally above it. Furthermore, the apartments slope above the water, which makes them difficult for firefighters to reach.'
DEDICATED TEST
EI refers to the flame-resistance (E) and thermal insulation (I). It is the criterion that measures the temperature rise of the glass on the protected side. The 30 per cent gentle slope of the window frames meant the glass had to be both fall-through resistant and walkable. The glass package is 74 millimetres in thickness. It has a Pyrobel T EI60 35H outside pane combined with an 888.8 laminated tempered-glass inner pane. The fire-resistant window is on the outside, where it would normally be used on the inside. This has to do with its walkability. The cavity with argon gas is 12 millimetres thick and the package has a UG value of about 1.1 W/m2K. The total area amounted to 140 square metres. As mentioned earlier, as standard, Jansen VISS Fire is suitable for vertical applications. Sloping structures need special testing, especially when the composition of the glass is different from usual.
Jan Liebeton is the Sales & Marketing Manager for Fire Resistant Glass of the Netherlands at AGC Glass Europe and explains why the test was done horizontally. 'The fire test was carried out at Efectis and the maximum size tested was 2,967 x 1,226 millimetres. This is a dedicated test, which was especially for this project with Kersten as the principal. If you test it vertically, you may only use the frame vertically for this specific composition with a deviation of 10 degrees. If you test it at 45 degrees, you can only do so with a slope of 15 to 80 degrees. When you do the test horizontally, you may do so for a slope of 0 to 80 degrees. This allows for wider scope for future use. This choice is partly based on the confidence in our product shown by both the contractor BESIX and MC Kersten. If you do not pass test, you have to take it again, which will cause a considerable delay. But all went well in one go and we passed it with over 90 minutes.'
CHALLENGING INSTALLATION
The precast frames with the thick glass package weigh about 600 kilograms and were too large and heavy to transport indoors. So, they had to be installed from the outside. The artist's impression of the end result showed the façades cantilevering out over the water. But there is just solid ground where the water will eventually be, so it is an 'ordinary' construction site. This made the installation of the frames somewhat easier although it was still a challenging job. Struik: 'We had to come up with a special installation method where we used a hoisting device. In fact, we lifted the frames from the ceiling through the façade into the homes. We designed the hoisting device in-house and also had it certified. It's seven storeys and we used a telescopic aerial platform for the first three storeys. Starting at the fourth storey, we were able to work using a mobile scaffold. And we also used a kind of grandstand scaffold from the contractor, which was there anyway as a supporting base for the concrete work.'
Results-oriented collaboration is a borrowed term that is used increasingly more in the construction industry. But where firms may be at odds with one another, it is Struik's job to get all parties onboard. 'Kersten was involved in the work from start to finish, design to completion,' he says, 'so, I'm a pivotal figure bringing work like this to a successful conclusion with all of our colleagues, suppliers, contractor, and architect. The cooperation with AGC in the preliminary, test, and implementation phases were also terrific. That's also what AGC is all about. They give advice based on their knowledge and expertise and are always great at providing support. An inherent thing with glass is that imperfections can occur. AGC resolves this competently and satisfactorily. The advantage in terms of manufacturing the steel structures is that we do the complete fabrication and assembly in-house, so if anything must be adjusted, we also do this in-house. We are always keep in mind agreements made also with AGC. So, the work went perfectly according to plan with a state-of-the-art result that we can all soon be proud of.'
PROJECT DETAILS
- Development: BESIX en VORM
- Principal: Municipality of Amsterdam
- Architect: Bjarke Ingels Group (BIG) and BARCODE Architects
- Main contractor: BESIX Nederland
- Fire-resistant frames: M.C. Kersten
- Fire-resistant glass: AGC Pyrobel
- Construction period: 2017 - 2022
- Total value: €70 million
- Capacity: 442 energy-efficient apartments and 4,000 m2 of commercial and/or communal spaces
- Size: 46,500 m2
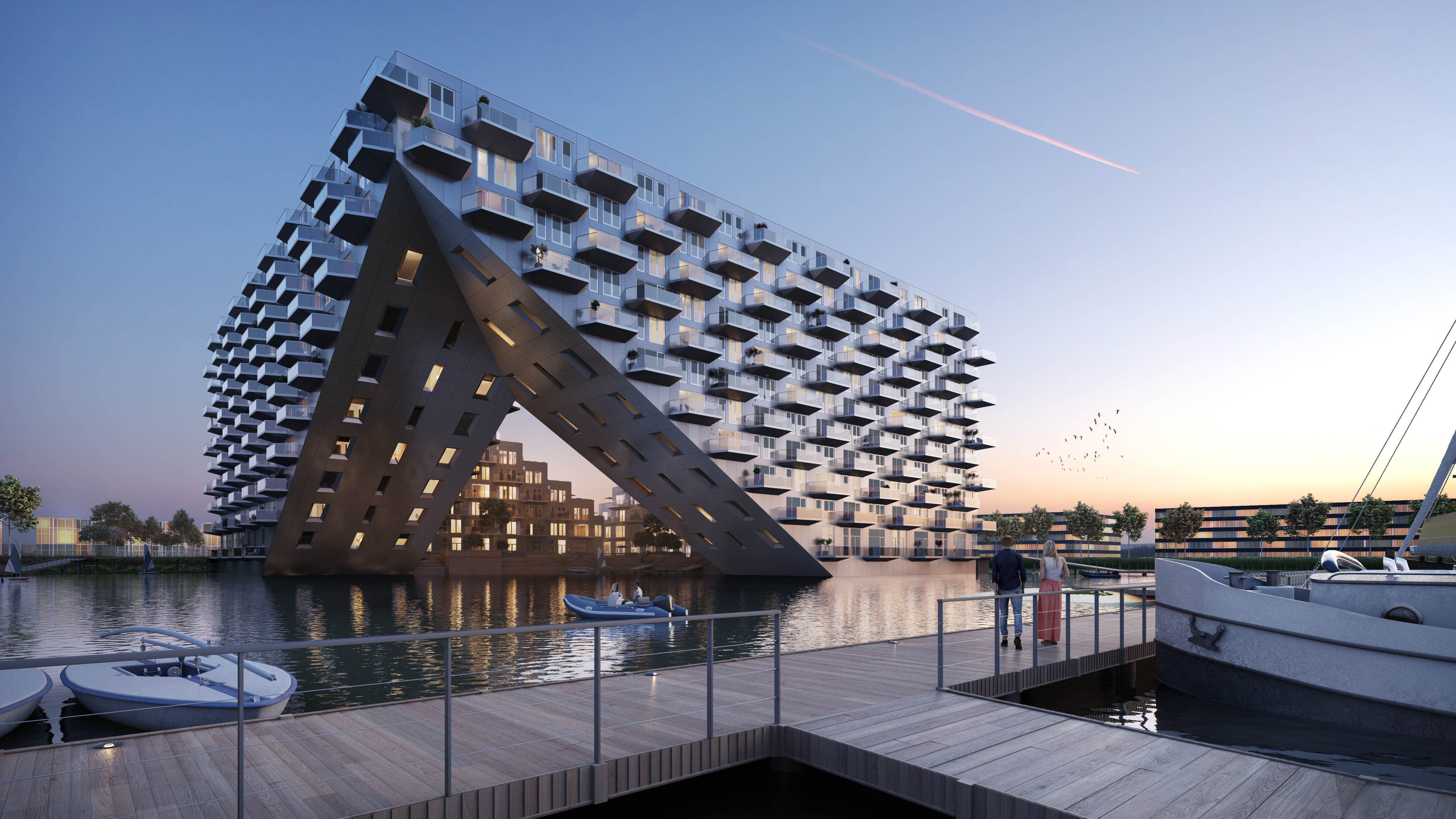
The windows of the cantilevered apartments with walkable fire-resistant glass with the highest classification (EI60). Artist impression: Barcode Architects
Jan Liebeton and Ronald Struik with a view of two sloping sections with fire-resistant glass in the background.
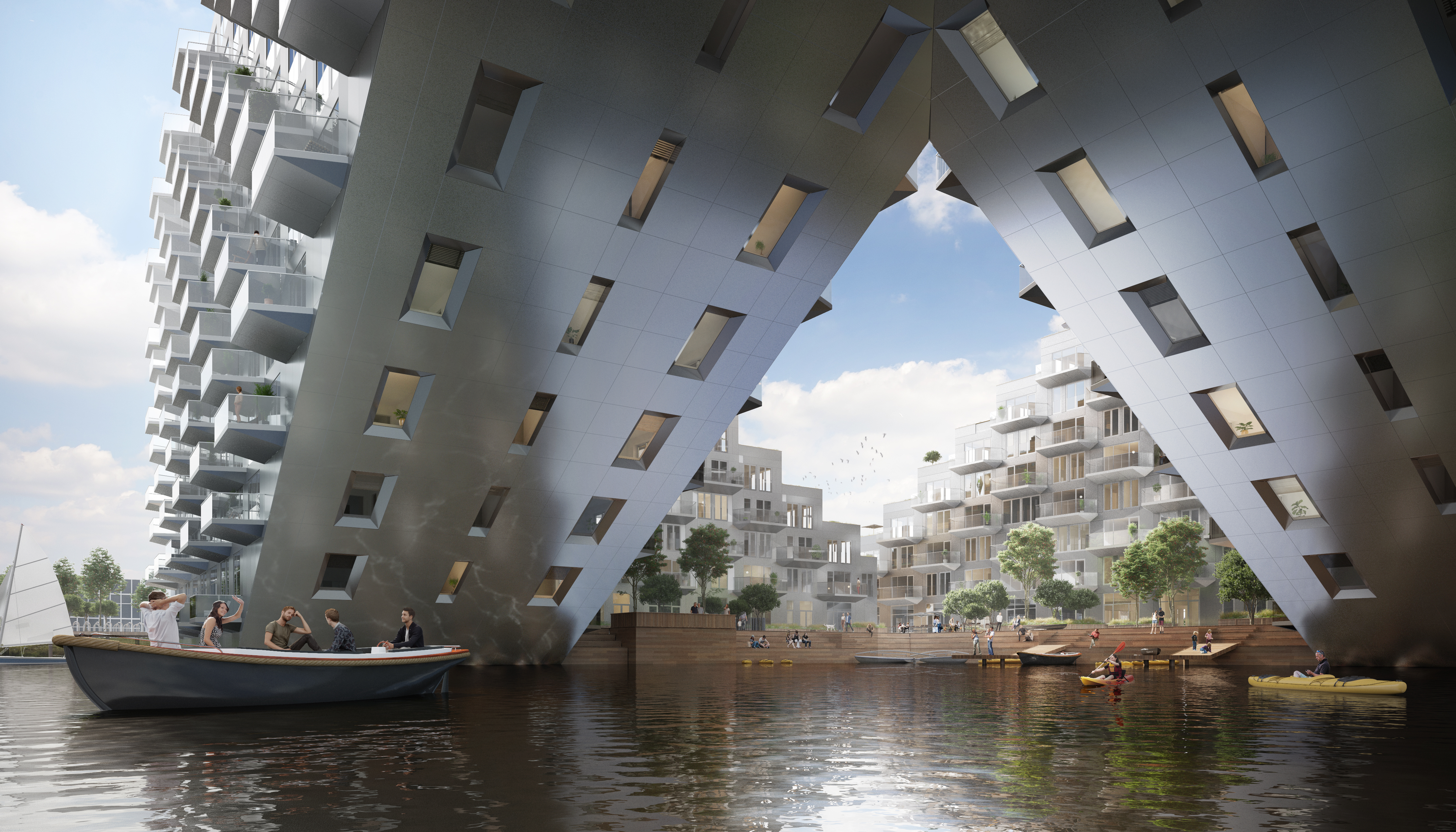
The floor plan is traditionally rectangular, but from every other point of view, the Sluishuis is completely asymmetric. Artist impression: Barcode Architects
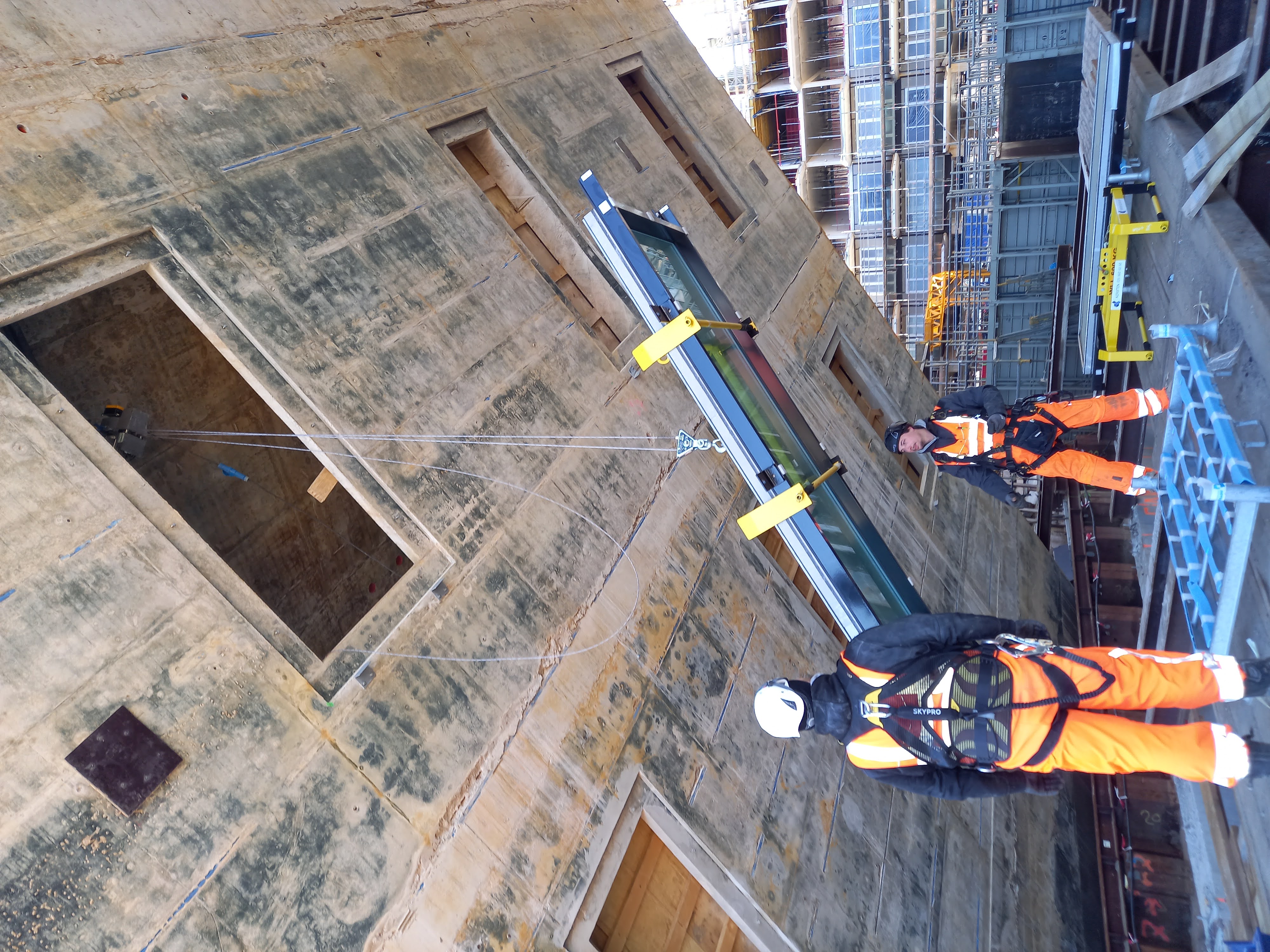
The precast window frames were lifted through the façade of the apartment ceilings using a special hoisting device.
Ronald Struik (left): 'The fire-resistant windows are walkable and in keeping with our series of special projects. It was a terrific collaboration with AGC Pyrobel.'
The Sluishuis is still under construction. Completion is scheduled for mid-2022.
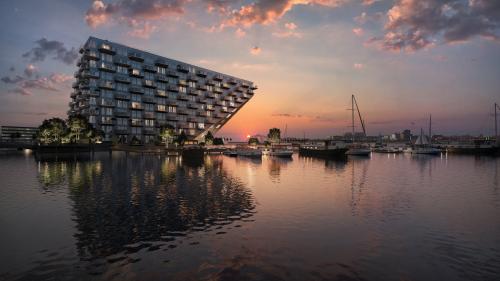
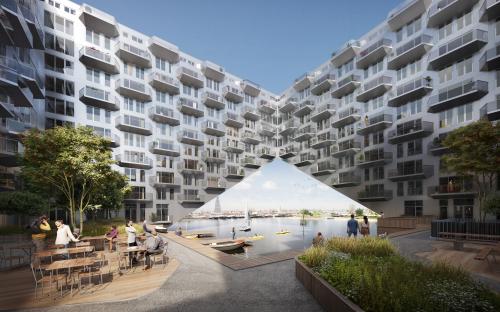
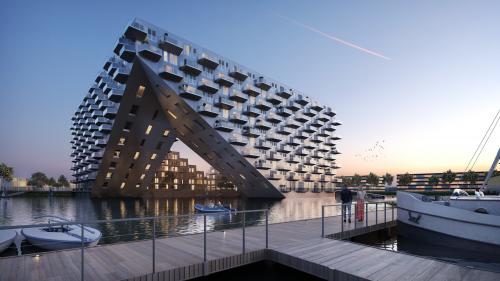